Critical Cleaning for Oxygen Service
Oxygen rich environments need to be scrupulously clean. Combustible hydrocarbon containing debris (such as oils, dust, paper, etc.) must be completely removed from your equipment. A spark or ignition inside a concentrated oxygen system can result in an explosion.
Dependent upon the starting condition of your system, there are a variety of methods and testing protocols that can be employed to meet the required standards. These are referenced in industry standard specifications such as: CGA G-4/1 and ASTM G-93 amongst others.
INOX Passivation are able to satisfy these requirements and certify your parts/system for oxygen use.
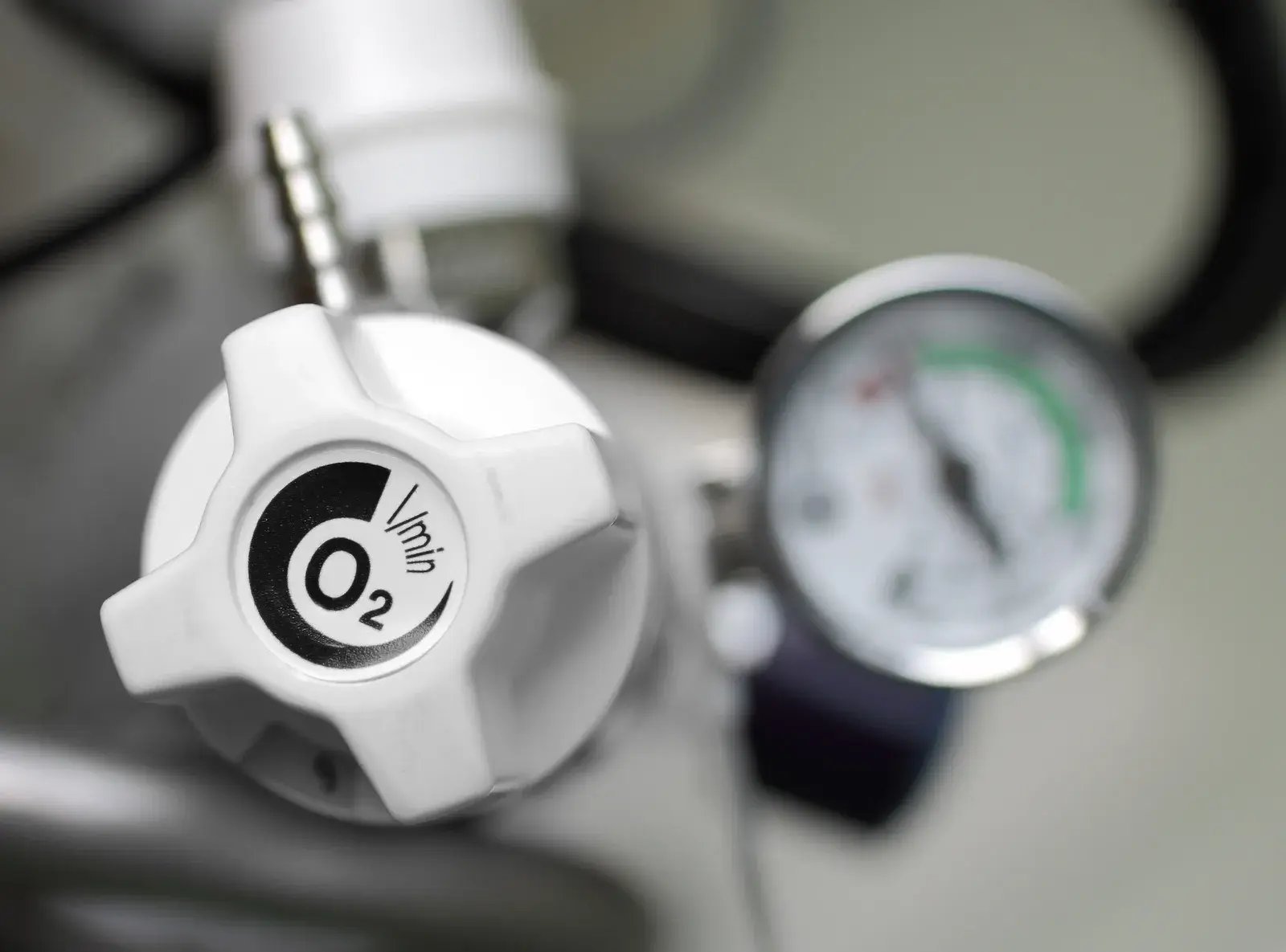
FAQs
“Oxygen cleaning” is effectively a very thorough cleaning operation of your storage and distribution systems that carry oxygen >22%. The intent is to remove all traces of products that could either cause, facilitate or feed a fire.
After chemical cleaning, the equipment is often dried to -40 o C dew-point before the system can be put into service.
No. There are various chemicals that can be used to achieve the cleanliness required. Their selection will be determined by the material(s) of your equipment, and the type / severity of any contamination. These are typically mild degreasers/cleaners.
There are various methods of inspection.
The simplest inspection is “Visual inspection” under white light and/or UV light. Many oils/hydrocarbons will fluoresce beneath an ultra-violet light, so contamination that wasn’t necessarily visible under the white light, can often be identified with UV.
This can be supplemented with a “swab test”. A white, lint-free cloth wetted with a suitable solvent is lightly wiped over the surface and inspected for discolouration.
Finally, a quantitative test – the “Solvent Extraction” test can be used. A measured volume of solvent is poured over a cleaned surface, collected, then analysed in a laboratory to determine the extent of any contamination it picked up. There are recommended limits - usually dependent on the oxygen % being stored.
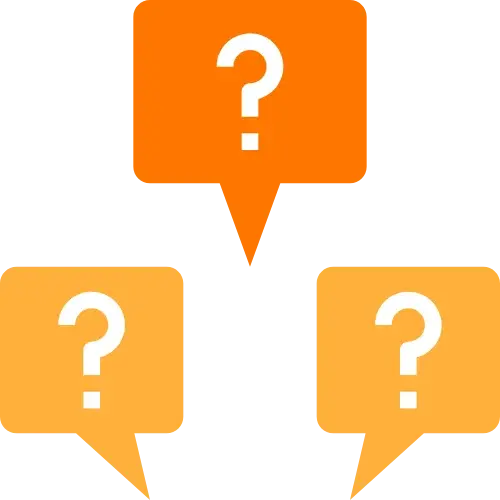
Speak To An Expert
Submit A Question Or Enquiry And Speak To One Of Our Experts To Find Out More!
Submit an enquiry with your question, to give us a brief or to request a call back from one of our experts.
When you get in touch with INOX:
We'll contact you back as soon as we are able to
We'll always aim to provide 'best advice' for your business
We offer a free initial consultation
Your information is treated in the strictest confidence
You can ask us for advice or help on any or all of the following:
- Passivation
- Derouging
- Oxygen Cleaning
- Biofilm Removal
- Riboflavin Testing
- Pre-Commissioning Flushing
- Carbon Steel Pickling
Simply confirm your details on the form provided and we'll be in touch ASAP. We look forward to hearing from you!
From Our Blog
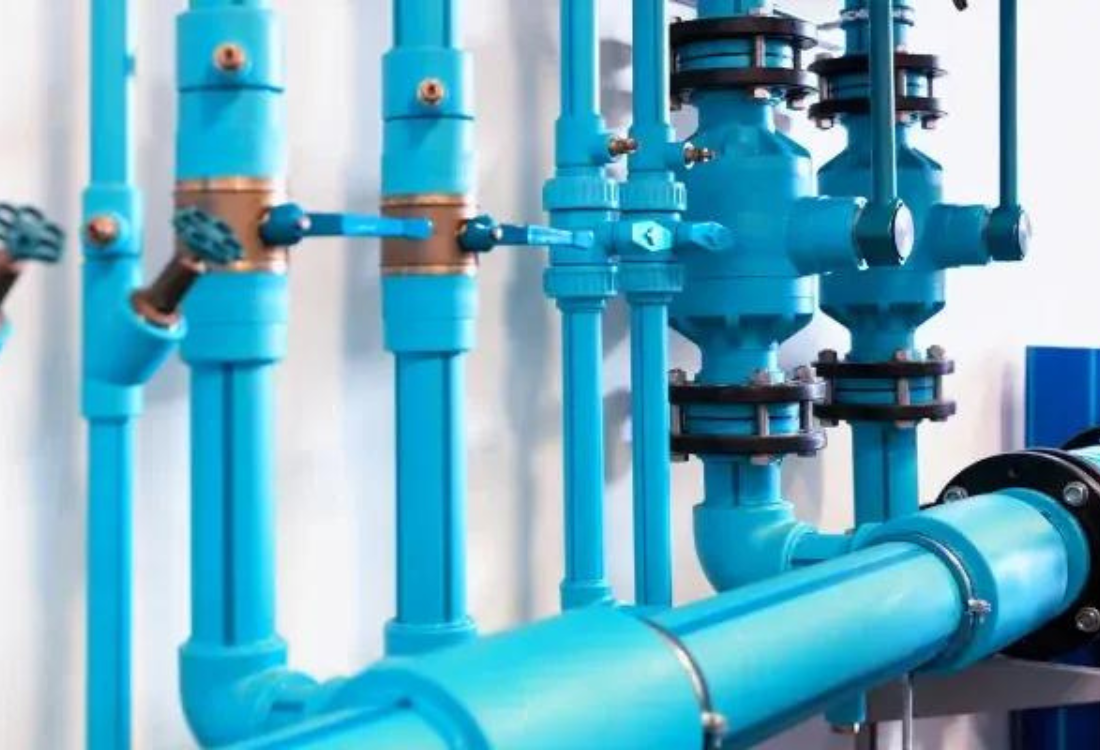
Benefits Of Stainless Steel Pickling In The Power Generation Industry
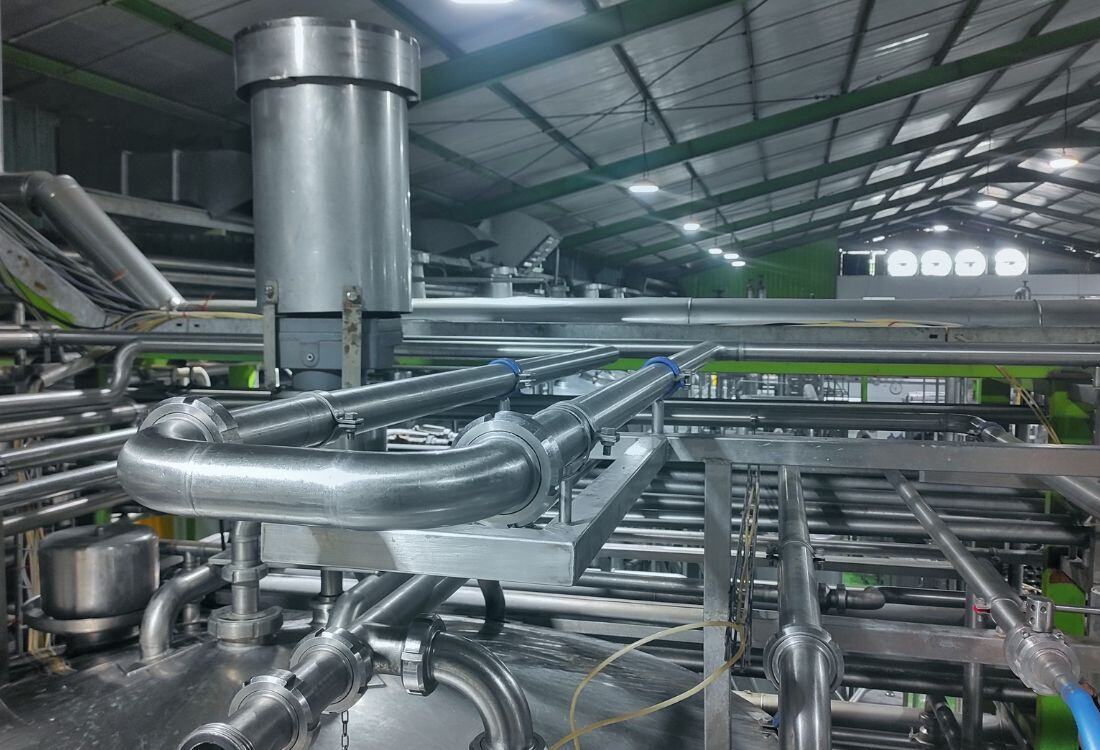
Rouge Types: What Are The Three Main Classes Of Rouge?
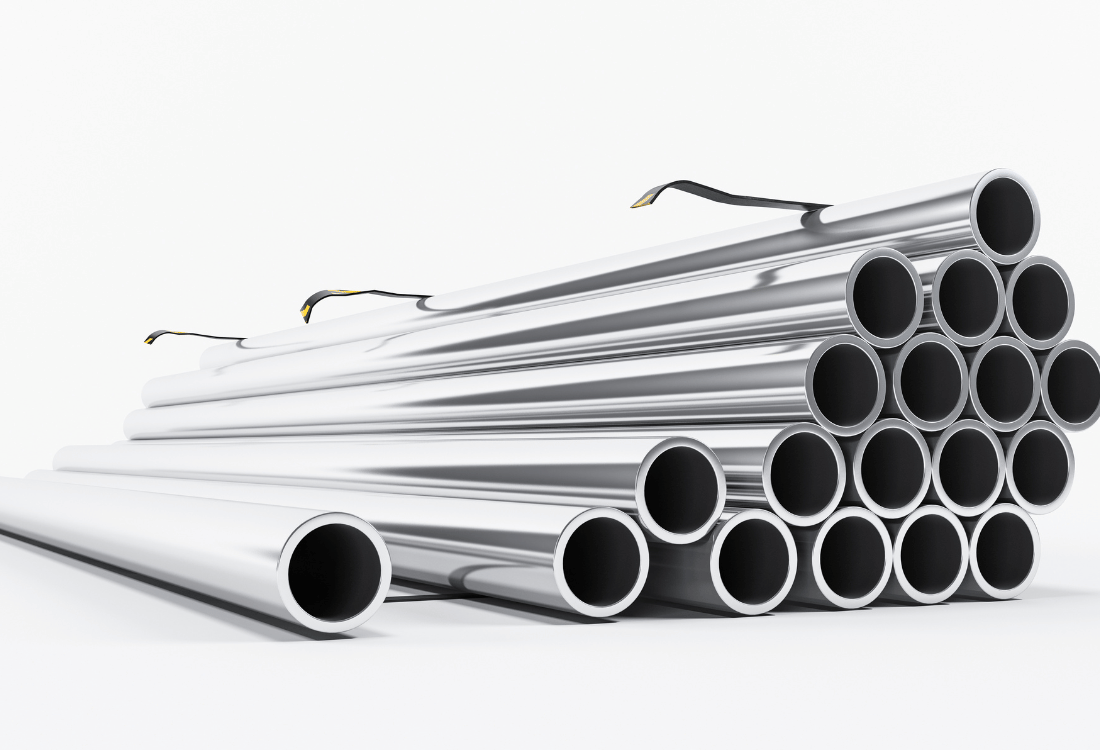